Tie-down lashing.
Tie-down lashing is the most common type of lashing for road goods transport, since most loads are so wide that securing can only be achieved by vertical or slightly inclined tie-down lashing. However, the following prerequisites must be observed for tie-down lashing:
- There must be a high level of friction between the load and the loading surface and between the loading units (plate transport). The dynamic friction factor µ must be known.
- The vertical angle α should be as close as possible to 90°. It must be known.
- The load must able to withstand a higher pre-tensioning.
- The lashing points must be suitable for the load.
- The most important factor, the size of the required pre-tensioning force that must be applied with the tensioning element, must be known.
This list shows the disadvantages and limits of tie-down lashing: During tie-down lashing, the lashing equipment, the lashing points and the load itself are permanently exposed to a high lashing force. In principle, however, tie-down lashing only works if, as mentioned above, there is a sufficiently high coefficient of friction between the loading area and the load. Steel on steel, for example, is very unfavourable, which is why wooden supports, friction-enhancing mats (anti-slip mats) or similar are used to increase friction. Obviously, the loading area and the load must be free of oil, dirt and ice.
How is the securing effect being generated during tie-down lashing?
The frictional force Fr is increased by applying the total tension force Fv in the lashing equipment (lashing chain, web lashing) by means of tensioning devices (load binder / ratchet-type load binder).
The actual friction force acting, also called the restraining force, is therefore made up of the proportion resulting from the dead weight of the load with G x µ and the part from the tension, which is calculated from the additionally applied tension force Fv x sin x µ. Both values together must be greater than the force with which the load tries to move on the loading area, i.e. 0.8 or 0.5 times the load weight:
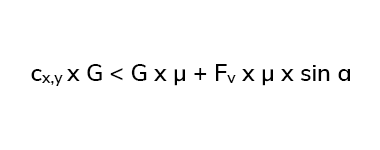
The following formula results for the required total pretensioning force Fv:
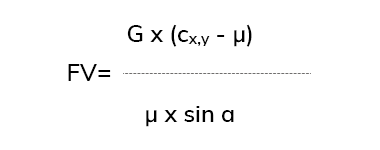
Here means:
G: weight force in daN ≈ mass m in kg
cx,y: acceleration factor
cx: acceleration factor in direction of travel = 0.8 / against the direction of travel = 0.5
cy: acceleration factor transverse to the direction of travel = 0.5
µ: dynamic friction factor
α: vertical angle (angle between loading area and chain strand)
Calculation example:
Load precast concrete element
m = 4000 kg ≈ 4000 daN = G
concrete/wooden loading area:
µ = 0,3
vertical angle α = 60°
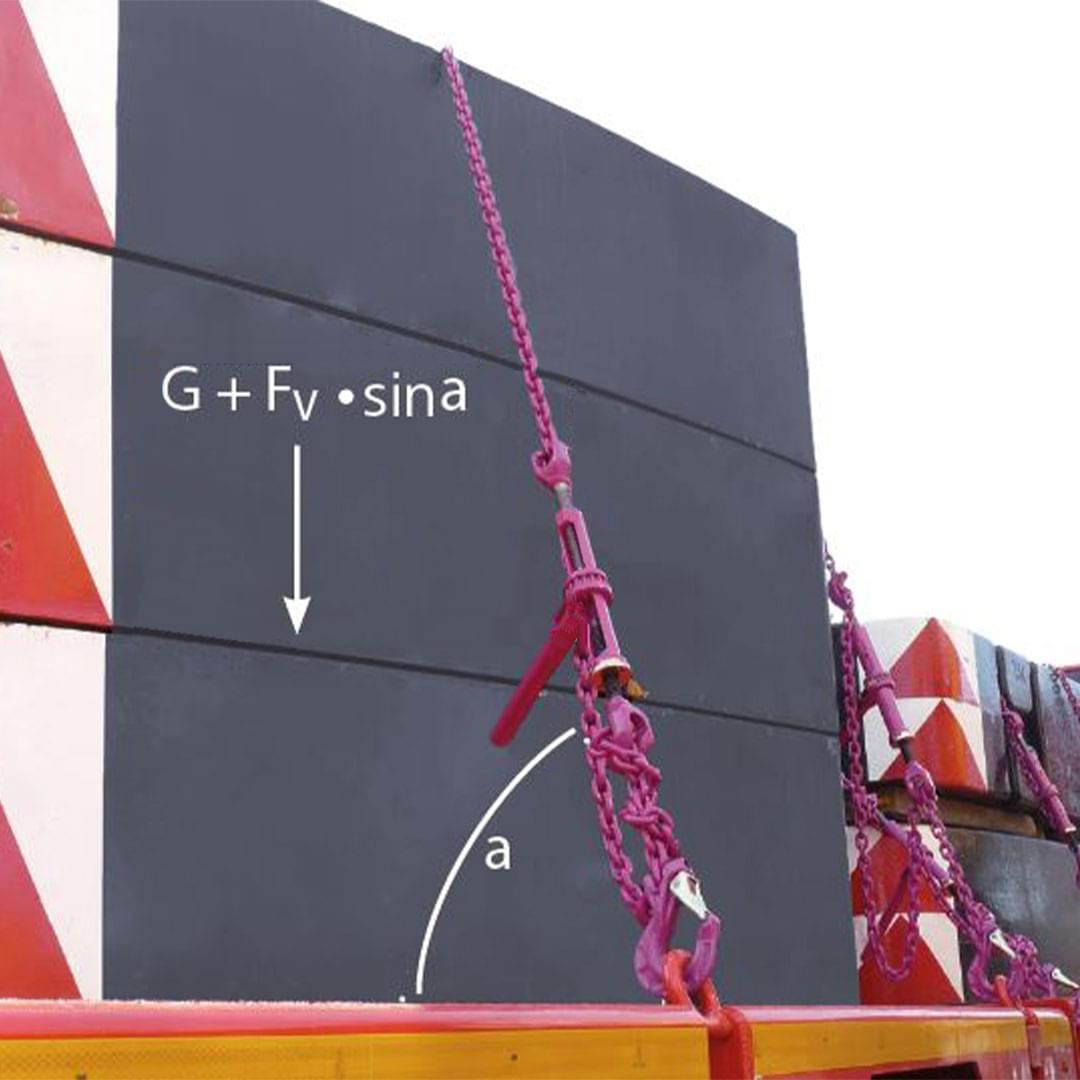
The basic idea of tie-down lashing is to increase the natural load by applying pre-tensioning forces and thus to increase the friction force which prevents the load from slipping.
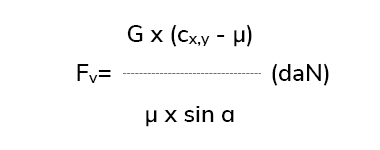
sin 60° = 0,866
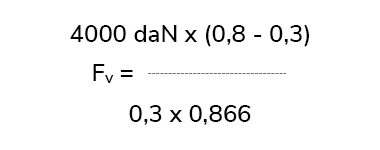
FV = 7698 daN (total pretensioning force)
This can be used to calculate the number of loop lashings n required:
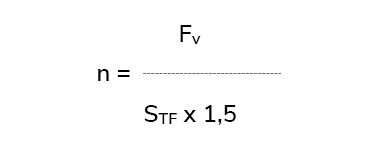
Here STF stands for standard tensioning force (the pretensioning force that can be achieved with a clamping element).
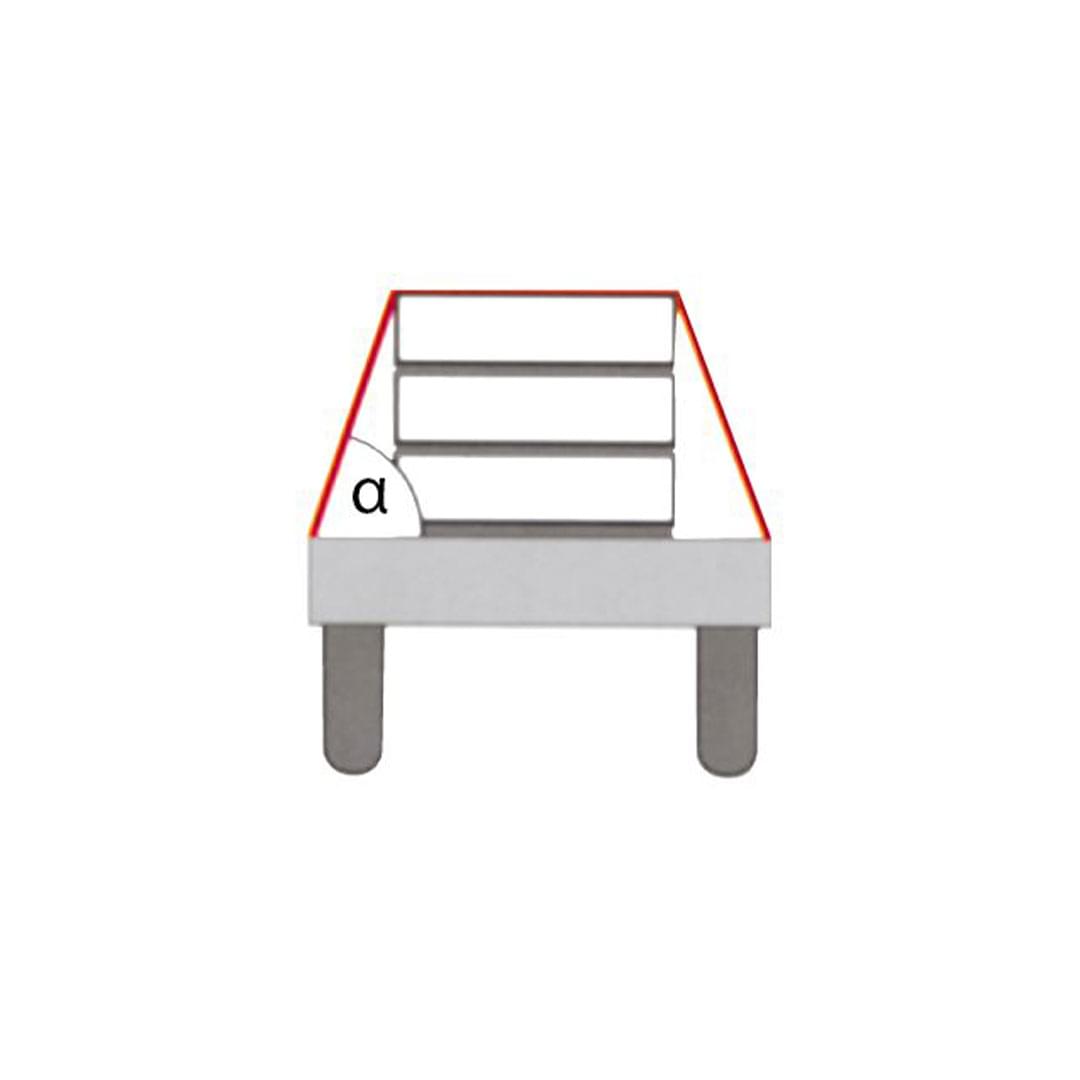
In the example, a RUD ICE lashing chain with a nominal thickness of 8 mm, with a STF of 2800 daN was selected.
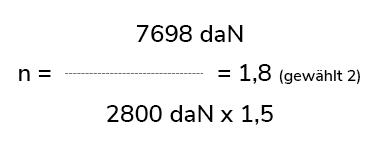
Result: Two lashing chains of the above type are required in the loop lashing for the lashing process.